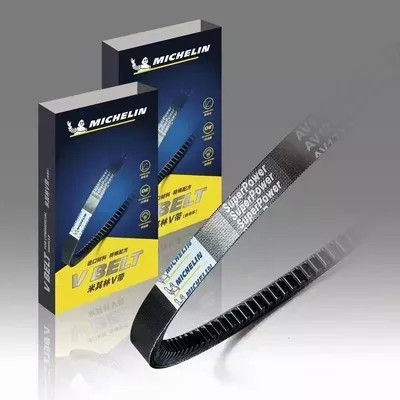
Common Materials for Industrial Belts: A Comprehensive Guide
Industrial belts are vital components across numerous industries. Choosing the right material for an industrial belt can significantly impact performance, efficiency, and durability. This guide provides an in-depth comparison of common materials used in industrial belts, detailing their properties and typical applications to help manufacturers make informed decisions.
Rubber Belts:
- Properties: High elasticity, excellent wear resistance, good shock absorption, flexible, cost-effective.
- Applications: Automotive industry (fan belts, timing belts), conveyor systems, general machinery, agricultural equipment, construction machinery.
- Advantages: Rubber belts are known for their flexibility and ability to absorb shocks, making them ideal for applications where vibration damping is important. They are also relatively inexpensive.
- Disadvantages: They have a limited temperature range and can degrade when exposed to oils and chemicals over time.
Polyurethane (PU) Belts:
- Properties: High wear resistance, excellent oil and chemical resistance, good elasticity, and durability.
- Applications: Food processing (due to hygienic properties), packaging industry, textile industry, automation equipment, printing industry.
- Advantages: PU belts are highly durable and resistant to abrasion, oil, and chemicals, making them suitable for harsh environments. They also maintain their shape and performance over time.
- Disadvantages: Higher cost compared to rubber belts, and they can be more challenging to splice and repair.
Nylon Belts:
- Properties: High tensile strength, good wear resistance, excellent heat resistance, low friction coefficient.
- Applications: Heavy machinery, high-temperature environments, industrial processing, automotive applications (timing belts, power transmission belts).
- Advantages: Nylon belts can withstand high temperatures and heavy loads, making them ideal for demanding industrial applications. They also have a low friction coefficient, which reduces energy consumption.
- Disadvantages: Absorb moisture, which can affect performance and dimensional stability.
Polyvinyl Chloride (PVC) Belts:
- Properties: Economical, resistant to chemicals, easy to clean, moderate temperature resistance.
- Applications: Material handling, light-duty applications, logistics, airport baggage systems, food and beverage industry (with appropriate coatings).
- Advantages: PVC belts are cost-effective and versatile, suitable for a wide range of light to medium-duty applications. They are also resistant to chemicals and easy to clean.
- Disadvantages: Not suitable for high-temperature applications, and they can become brittle over time.
Leather Belts:
- Properties: Natural flexibility, good grip, durable, biodegradable.
- Applications: Traditional machinery, woodworking, agricultural equipment, vintage equipment.
- Advantages: Leather belts provide a good grip and are naturally flexible, making them ideal for specific vintage or traditional machinery applications. They are also biodegradable.
- Disadvantages: Susceptible to moisture and chemical damage, limited by temperature and load capacity.
Fabric Belts:
- Properties: Lightweight, flexible, customizable, good tensile strength.
- Applications: Printing industry, textiles, lightweight conveying systems, packaging.
- Advantages: Fabric belts are highly flexible and lightweight, making them suitable for delicate or lightweight materials. They can also be customized to specific requirements.
- Disadvantages: Less durable compared to rubber or PU belts, and they can fray or wear quickly under heavy loads.
Metal Belts:
- Properties: High strength, extreme temperature resistance, durable, rigid.
- Applications: Metal processing, high-temperature ovens, heavy-duty conveyors, aerospace industry.
- Advantages: Metal belts can withstand extreme temperatures and heavy loads, making them ideal for demanding industrial and high-temperature applications.
- Disadvantages: High cost, heavy, and can be challenging to install and maintain.
Silicone Belts:
- Properties: Heat resistance, non-stick surface, chemical resistance, flexible.
- Applications: Baking industry, medical equipment, pharmaceuticals, food processing.
- Advantages: Silicone belts are highly resistant to heat and chemicals, and their non-stick surface makes them ideal for applications in the food and medical industries. They are also flexible and can be used in various configurations.
- Disadvantages: Higher cost compared to other materials, and they can be less durable under mechanical stress.
Application Recommendations
- High-Temperature Environments: Nylon and silicone belts are ideal due to their heat resistance.
- Oil and Chemical Resistance: Polyurethane belts offer excellent resistance.
- General Use and Cost-Effective Solutions: Rubber and PVC belts provide balanced performance and affordability.
- Heavy-Duty Applications: Metal belts are suitable for extreme conditions and heavy loads.
Conclusion
Selecting the right material for industrial belts is crucial for optimizing performance and longevity in various applications. Understanding the properties and typical uses of each material helps manufacturers make the best choices for their specific needs, ensuring efficient and reliable operation.
At Shin-Ho International Trade Co., Ltd., we offer a wide range of high-quality industrial belts to meet your specific requirements. For more detailed information and personalized recommendations, please visit our website or contact our sales team.